Table of Contents
ToggleIntroduction
In the dynamic world of manufacturing, CNC (Computer Numerical Control) machine tools play a pivotal role in ensuring precision and efficiency. As the demand for high-quality machining continues to rise, understanding the distinctions between different CNC configurations—specifically 3 Axis vs 4 Axis vs 5 Axis CNC machining—becomes crucial for manufacturers. This article aims to clarify these technologies, helping you make informed decisions regarding 3 Axis, 4 Axis, and 5 Axis CNC options for your production needs.
3-Axis CNC Machining
Definition and Key Features
axis CNC machining refers to the movement of the cutting tool along three different axes: X (horizontal), Y (vertical), and Z (depth). This configuration allows straightforward operations such as drilling, milling, and boring.
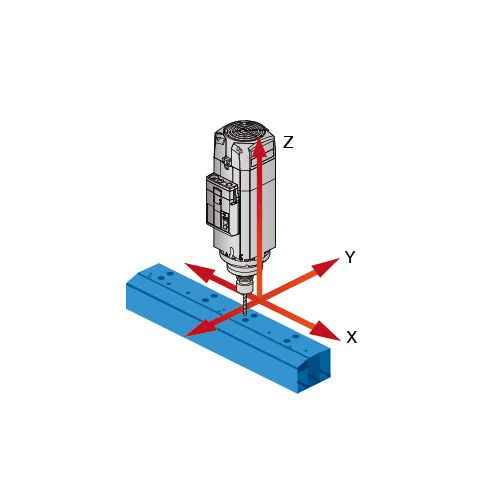
Advantages and Applications
- Simplicity: 3-axis machines are easier to program and operate, making them ideal for simple machining tasks.
- Cost-Effectiveness: Generally, 3-axis CNC machines are more affordable than their multi-axis counterparts, making them suitable for small to medium-sized businesses.
- Common Applications: Ideal for flat surfaces, 3D contours, and basic shapes, these machines are widely used in industries like woodworking, metalworking, and prototyping.
Limitations and Challenges
While 3-axis CNC machining is versatile, it has its limitations. Complex geometries and intricate designs often require additional setups or fixtures, which can lead to longer production times and increased costs.
4-Axis CNC Machining
Definition and Key Features
4-axis CNC machining adds a fourth rotational axis (A-axis) to the traditional three axes. This allows the workpiece to rotate, enabling the machine to access multiple sides without needing to reposition the part manually.
Currently, 99% of CNC systems support 4-axis linkage function,
So while processing, it can be more convenient to meet the processing needs of more complex parts.

Advantages and Applications
- Increased Efficiency: The ability to machine multiple sides of a workpiece in one setup reduces downtime and increases productivity.
- Enhanced Complexity: 4-axis machines can handle more complex geometries, making them suitable for industries like aerospace and automotive where precision is paramount.
- Common Applications: Ideal for creating complex shapes, 4-axis machining is often used for parts requiring intricate detailing, such as turbine blades and custom fittings.
Comparison with 3-Axis CNC Machining
While 3-axis machines are excellent for simpler tasks, 4-axis machines offer greater flexibility and efficiency for more complex projects. The choice between the two often depends on the specific requirements of the job and the desired level of detail.
5-Axis CNC Machining
Definition and Key Features
5-axis CNC machining introduces two additional rotational axes (B-axis and C-axis), allowing the cutting tool to approach the workpiece from virtually any angle. This capability significantly enhances the machine’s versatility.
When defining 5-axis machine tools, there are often misunderstandings. Many people mistakenly refer to them as 3+2 or 4+1 systems. However, for 5-axis machine tools, the key factor lies in the functionality of the CNC system rather than the structural design of the machine.
- Numerical Control System: Some systems only support 5-axis and 4-axis linkage. For example, the FANUC 0i series, Siemens 828D series, and HIRUNG’s EV series vertical machining centers come with standard configurations. These types of machine tools are typically referred to as the 4+1 series.
- 5-Axis Linkage: Systems such as Siemens ONE, GSK25i, and Heidenhain TNC640 support true 5-axis linkage. Any machine tool that supports 5-axis linkage, regardless of its structure, is considered a 5-axis machine tool. HIRUNG’s current offerings include the DV series 5-axis machine tools, DU series 5-axis machine tools, HPG series 5-axis gantry machine tools, and more.
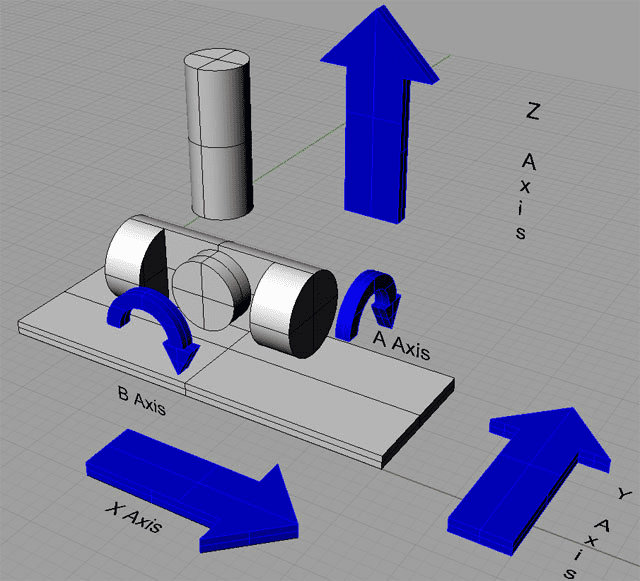
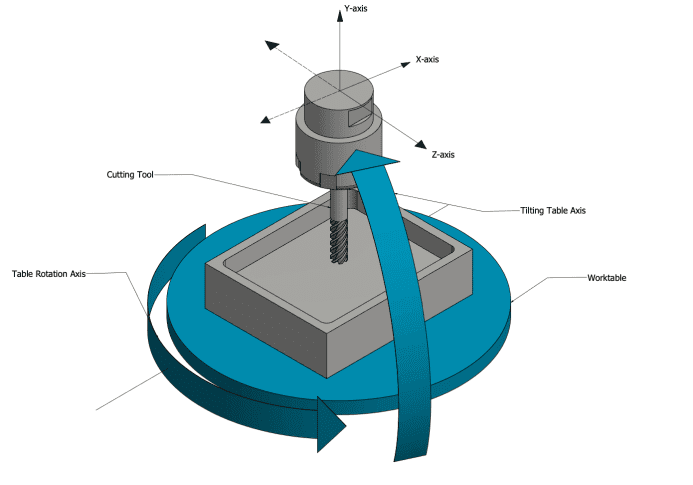
Advantages and Applications
- Unmatched Precision: 5-axis machining provides unparalleled accuracy, making it ideal for high-tolerance applications.
- Complex Designs: Capable of producing intricate parts in a single setup, reducing the need for multiple fixtures and setups.
- Common Applications: Widely used in industries like aerospace, medical device manufacturing, and high-end automotive parts, where precision and complexity are critical.
Comparison with 4-Axis CNC Machining
While 4-axis machines improve efficiency and complexity over 3-axis systems, 5-axis machines take it a step further by allowing for more intricate designs and reducing the need for part repositioning. This results in shorter production times and enhanced accuracy.
Choosing the Right CNC Machine
Factors to Consider
When selecting between 3-axis, 4-axis, or 5-axis CNC machines, consider the following factors:
- Complexity of Parts: Assess the complexity of the parts you need to produce. Simpler parts may only require a 3-axis machine, while more intricate designs may benefit from 4 or 5-axis capabilities.
- Production Volume: Higher production volumes may justify the investment in more advanced machines that offer efficiency and speed.
- Budget: Consider your budget and the potential return on investment. While 5-axis machines are typically more expensive, their efficiency may lead to cost savings in the long run.
CNC Machine Comparison Chart
Feature | 3-Axis CNC Machine | 4-Axis CNC Machine | 5-Axis CNC Machine |
Number of Axes | 3 | 4 | 5 |
Motion Directions | X, Y, Z | X, Y, Z + A (Rotational) | X, Y, Z + A (Rotational) + B, C (Rotational) |
Complexity of Parts | Suitable for Simple Shapes | Suitable for Moderate Complexity | Suitable for Complex Shapes and High Precision |
Production Efficiency | Lower, Requires Multiple Setups | Higher, Reduces Setup Time | Highest, Completes Multi-Sided Machining in One Setup |
Programming Difficulty | Simple | Moderate | More Complex |
Applicable Industries | Woodworking, Metalworking, Prototyping | Aerospace, Automotive, Custom Parts | Aerospace, Medical Devices, High-End Automotive Parts |
Cost | Lower | Moderate | Higher |
Common Applications | Flat Machining, Simple Contours | Complex Shapes, Multi-Sided Parts | High-Precision Parts, Intricate Geometries |
HIRUNG: A Leader in High-Quality CNC Machine Tools
At HIRUNG, we pride ourselves on our commitment to manufacturing excellence. Our CNC machines are designed with stability and quality in mind, ensuring that you receive the most reliable tools for your operations. With a proven track record of over 1,000 machines sold and a minimal failure rate of fewer than 20 notifications per year, we stand out as a trusted brand in the industry.
Our global presence in 33 countries reflects our dedication to quality and customer satisfaction. We understand that when investing in CNC machine tools, reliability is paramount. That’s why we promise the fastest solutions to any issues that may arise with our machines, ensuring your operations run smoothly.
Conclusion
In summary, understanding the differences between 3 Axis vs 4 Axis vs 5 Axis CNC machining is essential for making informed decisions in manufacturing. Each configuration offers unique advantages and is suited for different applications. By carefully considering your production needs and the specific requirements of your projects, you can select the right CNC machine to enhance efficiency and precision.
As you explore your options in 3 Axis vs 4 Axis vs 5 Axis CNC technologies, consider HIRUNG as your partner in high-quality CNC machine tools. With our commitment to excellence and customer satisfaction, we are here to support your manufacturing journey. Contact us today to learn more about our products and how we can help you achieve your machining goals.