In the world of manufacturing, two essential processes that play a critical role in shaping and modifying materials are vertical milling and drilling. Both techniques are widely used in various industries, but they serve different purposes and are employed for different types of operations. In this article, we’ll explore what vertical milling and drilling are, their key differences, applications, advantages, and disadvantages, and how to decide which process best suits your project.
Overview of Vertical Milling
What is Vertical Milling?
Vertical milling refers to a process where the cutting tool, typically an end mill, is mounted vertically on a spindle that moves along various axes. This orientation allows the tool to cut into the material, typically metal or plastic, from above. Vertical milling machines are often used for operations like face milling, slotting, drilling, and contour milling.
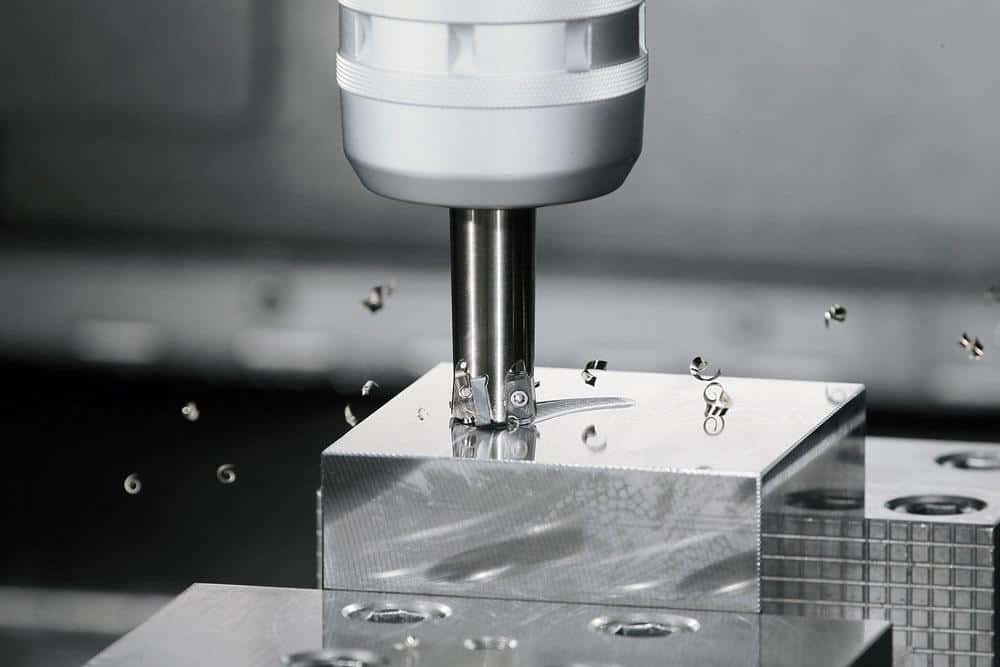
Applications of Vertical Milling
Vertical milling is incredibly versatile and used in industries that demand high precision and complexity. In automotive, aerospace, and medical device manufacturing, vertical milling is used to create intricate shapes, slots, holes, and surface finishes on a wide variety of materials. For example, automotive parts such as engine blocks or precision medical implants can be manufactured with vertical milling, as it provides superior control over part geometry.
Overview of Drilling
What is Drilling?
Drilling is a cutting process used to create round holes in solid materials, usually metals or plastics. The operation is typically done with a rotating drill bit that cuts into the material, removing chips to form a hole. Drilling machines are simple to use, primarily focused on the task of hole creation, and vary in complexity based on the scale and requirements of the hole being drilled.

Applications of Drilling
Drilling is a primary function in nearly every manufacturing industry. It is commonly used in construction, aerospace, automotive, and electrical industries to create holes for fasteners, fittings, or pipes. For example, in electronics manufacturing, drilling is crucial for creating holes in circuit boards for electrical components.
Key Differences Between Vertical Milling and Drilling
Function and Purpose
While both vertical milling and drilling are used to cut into a material, their functions are distinct. Vertical milling is a more versatile process that can be used for cutting surfaces, slots, and even creating 3D contours. Drilling, on the other hand, is specialized for creating holes and is not generally used for other types of machining operations.
In simple terms:
- Vertical Milling: Used for shaping surfaces, slots, and more complex geometries.
- Drilling: Focused solely on creating holes.
Machines and Tools
The machines used in vertical milling and drilling also differ significantly. Vertical milling machines are equipped with a rotating spindle that can hold various tools like end mills, which allow for precision cutting on multiple surfaces. Drilling machines, however, are generally simpler, utilizing a rotating drill bit specifically designed to create holes in the material.
- Vertical Milling Tools: End mills, face mills, and ball mills.
- Drilling Tools: Twist drill bits, spade drills, and reamers.
Speed, Precision, and Flexibility
Drilling is typically faster than milling, as it involves simpler, more direct operations. Vertical milling, being a more complex process, takes longer but offers higher precision and versatility. Milling allows for adjustments in speed, cutting angles, and tool changes, providing more flexibility in operations.
- Drilling: Faster for creating holes, but less versatile.
- Vertical Milling: Slower, but offers higher precision and more versatile operations.
Advantages and Disadvantages of Vertical Milling vs. Drilling
Advantages of Vertical Milling
- Versatility: Can perform a variety of operations, including cutting, drilling, and shaping.
- Precision: Capable of creating intricate and detailed designs with high accuracy.
- Complex Geometry: Ideal for creating complex shapes, including contoured surfaces and angular cuts.
Advantages of Drilling
- Speed: Drilling operations are typically quicker than milling.
- Simplicity: Drill bits are easy to replace, and drilling machines are simple to operate.
- Cost-Effective: Drilling can be a more cost-effective option when only hole creation is required.
Disadvantages of Vertical Milling
- Cost: Milling machines tend to be more expensive than drilling machines.
- Complexity: Milling requires more expertise and can be slower for simple operations.
Disadvantages of Drilling
- Limited Applications: Drilling is only suitable for creating holes and cannot handle other types of machining operations.
- Less Precision for Complex Parts: Drilling can’t create the detailed geometry that milling can achieve.
Choosing Between Vertical Milling and Drilling
Factors to Consider
When deciding between vertical milling and drilling, consider factors like the type of part, material, and complexity of the task. For projects requiring only hole creation, drilling is the best option. However, if your project involves creating precise surfaces, slots, or intricate parts, vertical milling is the better choice.
When to Use Vertical Milling
Vertical milling is the preferred method for parts that require complex shapes, precise surface finishes, and intricate geometry. Use vertical milling when you need to perform tasks such as:
- Creating multi-faceted parts.
- Cutting complex shapes like slots or gears.
- High-precision work requiring tight tolerances.
When to Use Drilling
Drilling is the ideal solution when you need to create holes quickly and efficiently. It is the preferred method for:
- Creating round holes in various materials.
- Simpler, straightforward operations.
- Cost-effective and quick manufacturing processes.
Conclusion
In conclusion, both vertical milling and drilling are essential processes in manufacturing, each with its unique set of advantages. Vertical milling is highly versatile and ideal for intricate parts and complex surfaces, while drilling excels at quickly creating holes in a variety of materials.
At DONGGUAN HIRUNG PRECISION MACHINERY CO., LTD, we specialize in providing high-quality CNC machines that offer both vertical milling and drilling capabilities. Our machines are designed to provide precision, efficiency, and reliability to support your manufacturing needs. Whether you require complex milling operations or simple hole creation, our advanced solutions can help improve your production processes and achieve your desired outcomes.
For more information, feel free to contact us and explore how our high-end CNC machines can benefit your business.