I. Introduction
In the realm of modern manufacturing, Computer Numerical Control (CNC) lathes stand as pivotal machines that transform raw materials into precise and complex components. These versatile machines are integral to industries ranging from automotive to aerospace, where precision and efficiency are paramount. At the heart of enhancing CNC lathe capabilities lie live tools—innovative attachments that expand the functionality of traditional lathes, enabling multi-axis machining and reducing the need for secondary operations.
This article delves into the various types of live tools used in CNC lathes, exploring their functionalities, benefits, and applications. Whether you’re a seasoned machinist or new to CNC operations, understanding live tools can significantly impact your manufacturing processes, leading to increased productivity and superior product quality.
II. Understanding CNC Lathe Live Tools
Before exploring the types of live tools, it’s essential to grasp what they are and how they differ from standard lathe tools.
Definition of Live Tools in CNC Lathes
Live tools are powered tools integrated into CNC lathes, allowing for simultaneous operations along multiple axes. Unlike traditional lathe tools that are fixed and primarily operate in the X and Z axes, live tools can rotate and move independently, facilitating tasks such as milling, drilling, and tapping directly on the lathe without the need for separate machinery.
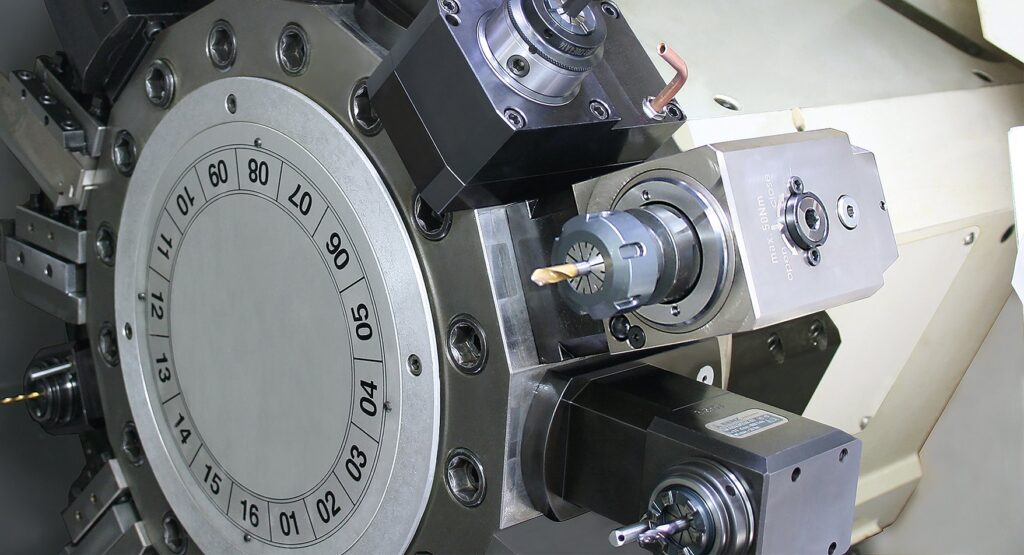
Comparison Between Live Tools and Standard Lathe Tools
Standard lathe tools are typically static, limited to cutting along specific axes, and often require manual adjustments or separate machines for complex operations. In contrast, live tools are dynamic, controlled by the CNC system, and capable of performing a variety of tasks in a single setup. This integration not only streamlines the manufacturing process but also enhances precision and reduces production time.
Advantages of Using Live Tools in CNC Machining
- Increased Productivity: Perform multiple operations in one setup, minimizing machine idle time.
- Enhanced Precision: Reduced manual handling leads to fewer errors and higher accuracy.
- Cost Efficiency: Lower operational costs by eliminating the need for additional machinery and labor.
- Flexibility: Ability to handle complex geometries and multi-axis machining with ease.
III. Types of Live Tools in CNC Lathes
CNC lathes can be equipped with various types of live tools, each serving distinct purposes to augment machining capabilities. Here’s an in-depth look at the primary types:
A. Live Tool Spindles
Description and Functionality
Live tool spindles are essentially motorized tool holders integrated into the CNC lathe. They rotate independently of the main spindle, allowing tools to perform cutting operations on multiple axes simultaneously. These spindles can be programmed to adjust speed and torque based on the machining requirements.
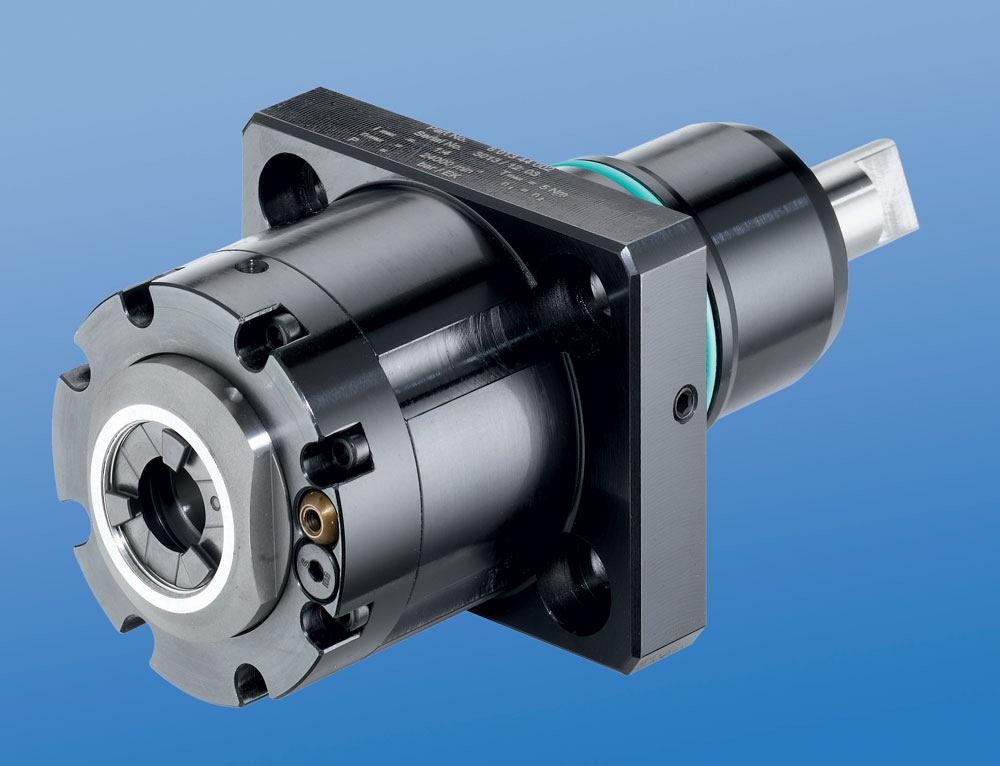
Common Applications
- Milling Operations: Performing milling tasks such as slotting, drilling, and pocketing.
- Drilling and Tapping: Creating precise holes and threads without repositioning the workpiece.
- Grooving: Cutting grooves or channels into the workpiece for various applications.
B. Tool Changers
Automated Tool Changing Mechanisms
Tool changers automate the process of switching between different tools during a machining cycle. They store a variety of tools and, under CNC control, select and position the appropriate tool as needed. This automation eliminates manual tool changes, reducing downtime and enhancing efficiency.
Benefits in Production Efficiency
- Reduced Setup Time: Quick tool changes minimize machine idle periods.
- Enhanced Workflow: Seamless transitions between operations maintain a steady production flow.
- Increased Tool Variety: Ability to handle a broader range of operations without manual intervention.
C. Live Tool Extensions
Purpose and Use-Cases
Live tool extensions are attachments that extend the reach of live tools, allowing access to deeper or more intricate areas of the workpiece. They provide additional length and flexibility, enabling machining of complex geometries that standard tools might not reach.
Impact on Machining Flexibility
- Access to Tight Spaces: Ability to machine areas that are otherwise inaccessible.
- Enhanced Reach: Increased tool travel range for more comprehensive machining tasks.
- Versatility: Supports a wider array of machining operations without changing the setup.
D. Live Tool Coolant Systems
Integration of Coolant Delivery with Live Tools
Live tool coolant systems integrate coolant delivery directly into the live tools, ensuring consistent and precise application of coolant during machining operations. This integration helps in maintaining optimal cutting temperatures and reducing thermal deformation.
Advantages in Heat Management and Tool Longevity
- Improved Cutting Performance: Effective heat dissipation enhances tool performance and surface finish.
- Extended Tool Life: Reduced thermal stress minimizes tool wear and extends lifespan.
- Enhanced Safety: Proper coolant management prevents overheating and potential machine damage.
E. Rotary Tables and Indexers
Enhancing Multi-Axis Machining Capabilities
Rotary tables and indexers are live tools that allow the workpiece to be rotated and indexed precisely during machining. This capability is crucial for complex parts that require multiple angles or positions to be machined accurately.
Typical Applications in Complex Part Manufacturing
- Multi-Faceted Components: Machining parts with multiple flat or angled surfaces.
- Threaded Components: Creating threaded sections at various orientations.
- Intricate Designs: Producing detailed and complex geometries with high precision.
IV. Selecting the Right Live Tool for Your CNC Lathe
Choosing the appropriate live tools for your CNC lathe is pivotal to maximizing efficiency and achieving desired machining outcomes. Here are key factors to consider:
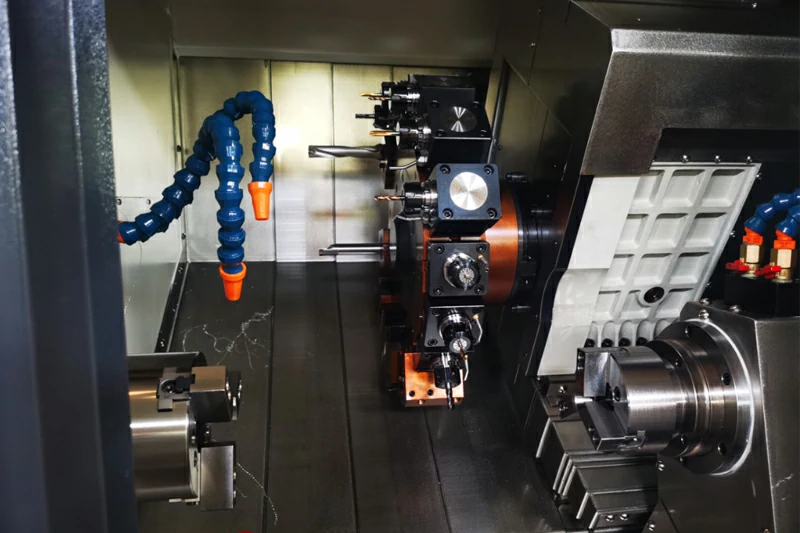
Factors to Consider
- Machining Requirements: Assess the types of operations you need to perform—milling, drilling, tapping, etc.
- Material Type: Different materials may require specific tool types and configurations.
- Production Volume: High-volume production may benefit from automated tool changers and robust live tools.
Compatibility with Existing CNC Lathe Systems
Ensure that the live tools you select are compatible with your CNC lathe’s control system, spindle specifications, and power requirements. Compatibility ensures seamless integration and optimal performance.
Cost-Benefit Analysis
Evaluate the initial investment against the long-term benefits such as increased productivity, reduced labor costs, and enhanced product quality. Investing in high-quality live tools can lead to significant returns through improved operational efficiency.
V. Maintenance and Best Practices for Live Tools
Proper maintenance is essential to ensure the longevity and optimal performance of live tools. Adhering to best practices can prevent common issues and extend the life of your equipment.
Regular Maintenance Schedules
- Routine Inspections: Regularly check for wear, damage, or misalignment.
- Cleaning: Keep tools and components free from debris and coolant residue.
- Lubrication: Ensure moving parts are adequately lubricated to prevent friction and wear.
Common Issues and Troubleshooting
- Tool Wear: Monitor tool edges for signs of wear and replace as necessary.
- Alignment Problems: Misaligned tools can lead to inaccuracies; recalibrate regularly.
- Coolant Blockages: Ensure coolant systems are free from blockages to maintain effective cooling.
Tips for Prolonging Tool Life and Ensuring Optimal Performance
- Use Appropriate Cutting Parameters: Optimize speed, feed, and depth of cut based on material and tool specifications.
- Avoid Overloading: Prevent excessive loads that can strain the tools and machine.
- Training: Ensure operators are well-trained in using and maintaining live tools effectively.
VI. Future Trends in CNC Lathe Live Tools
The landscape of CNC machining is continually evolving, with innovations driving advancements in live tool technology.
Innovations in Live Tool Technology
- Smart Tools: Integration of sensors and IoT capabilities for real-time monitoring and predictive maintenance.
- Advanced Materials: Development of tools made from new materials offering higher durability and performance.
- Adaptive Control Systems: Enhanced CNC controls that automatically adjust tool parameters for optimal machining.
Impact of Automation and Industry 4.0 on Live Tool Development
Industry 4.0 emphasizes automation, data exchange, and smart manufacturing. Live tools are becoming more intelligent, with capabilities to communicate data, adapt to changing conditions, and integrate seamlessly into automated production lines.
Predictions for the Future of CNC Machining
- Increased Automation: Greater reliance on automated live tools for higher efficiency and reduced human intervention.
- Enhanced Precision: Advances in tool technology leading to even higher levels of precision and surface finish.
- Sustainability Focus: Development of energy-efficient live tools and processes to support sustainable manufacturing practices.
VII. Conclusion
Live tools have revolutionized CNC lathe operations, offering unparalleled flexibility, precision, and efficiency. By understanding the various types of live tools available and selecting the right ones for your specific needs, you can significantly enhance your manufacturing capabilities. Regular maintenance and staying abreast of technological advancements will ensure that your CNC lathe remains a cornerstone of your production process, delivering high-quality components with consistency and reliability.