Vertical Machining Centers (VMCs) are a cornerstone of modern manufacturing. These computer numerically controlled (CNC) machine tools offer a powerful combination of precision, versatility, and efficiency, making them indispensable for a wide range of industries. From aerospace and automotive to medical and consumer goods, VMCs play a crucial role in producing complex parts with high accuracy. This article delves into the advantages and disadvantages of VMCs to provide a comprehensive understanding of their capabilities and limitations.

Advantages of VMCs
VMCs offer several key advantages that contribute to their widespread adoption in various manufacturing settings:
1. High Precision and Accuracy
VMCs excel in producing parts with exceptional precision and accuracy. The CNC control system allows for precise movements along multiple axes, ensuring consistent results across large production runs. This high level of accuracy is essential for creating intricate parts with tight tolerances, particularly in industries like aerospace and medical device manufacturing.
2. Increased Productivity and Efficiency
Automation is a key benefit of VMCs. Once programmed, they can operate continuously with minimal human intervention, significantly increasing production rates compared to manual machining methods. This automation also reduces human error, leading to higher consistency and less material waste. Faster machining speeds and tool changes further enhance productivity.
3. Versatility and Flexibility
VMCs can perform a variety of machining operations, including milling, drilling, tapping, and boring, all on a single machine. This versatility reduces the need for multiple specialized machines, saving floor space and setup time. The ability to quickly reprogram the machine for different parts allows for greater flexibility in handling diverse production needs.
4. Improved Safety
The automated nature of VMCs enhances workplace safety. Operators are less exposed to moving parts and cutting tools than with manual machines. Enclosed work areas and safety interlocks further minimize the risk of accidents.
5. Cost-Effectiveness
While the initial investment in a VMC can be substantial, the long-term cost benefits can be significant. Increased productivity, reduced labor costs, lower material waste, and minimized tooling expenses contribute to a lower overall cost per part, especially in high-volume production.
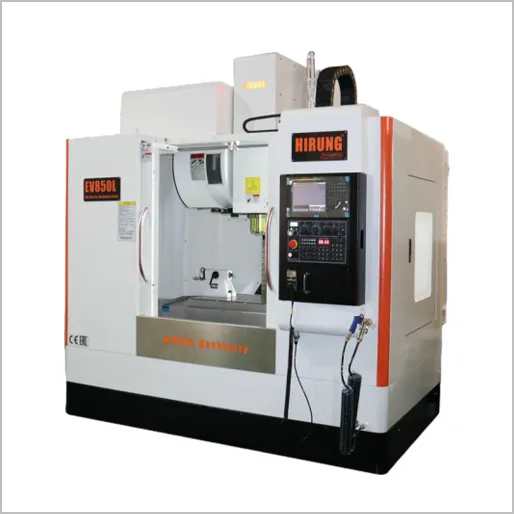
Disadvantages of VMCs
Despite their many advantages, VMCs also have some drawbacks that need to be considered:
1. Higher Initial Investment
The initial cost of purchasing a VMC can be a significant barrier, especially for smaller businesses. This investment includes not only the machine itself but also associated costs like tooling, software, and installation.
2. Skilled Operator Requirement
While VMCs automate many tasks, skilled operators are still required to program, operate, and maintain the machines. Finding and training qualified personnel can be a challenge. The complexity of the software and the need for precise programming require a higher level of technical expertise.
3. Maintenance and Repair
VMCs are complex machines with many intricate components. Regular maintenance is essential to ensure optimal performance and prevent costly breakdowns. Specialized technicians are often required for repairs, which can lead to downtime and additional expenses.
4. Size and Weight Restrictions
VMCs have limitations on the size and weight of the workpieces they can handle. The physical dimensions of the machine’s work envelope dictate the maximum size of the part that can be machined. Similarly, the machine’s weight capacity limits the weight of the workpiece.
5. Software Complexity
The software used to program VMCs can be complex and require specialized training to master. Programming errors can lead to scrapped parts and lost production time. Keeping the software up-to-date can also be an ongoing expense.
Choosing the Right VMC
Selecting the right VMC involves careful consideration of various factors, including the specific machining requirements, budget constraints, available floor space, and the skill level of the operators. It’s essential to choose a machine that meets the present needs while also allowing for future growth and expansion.
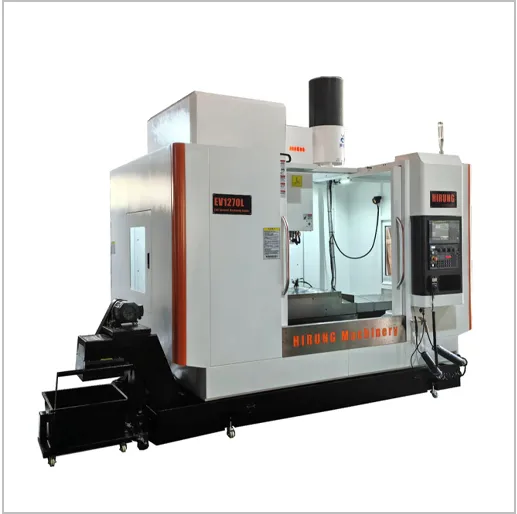
Conclusion
VMCs are powerful and versatile machine tools that offer significant advantages in terms of precision, productivity, and flexibility. However, they also come with certain limitations, such as higher initial investment costs and the need for skilled operators. Carefully weighing the advantages and disadvantages is crucial in determining whether a VMC is the right solution for your specific manufacturing needs.
At HIRUNG, we understand the complexities of choosing the right machining equipment. We are committed to manufacturing high-quality CNC machine tools that deliver precision and reliability. With a focus on customer satisfaction and a dedication to continuous improvement, we strive to provide our clients with the best machining solutions for their individual requirements. Contact us to learn more about how HIRUNG can help optimize your manufacturing processes.