1. Introduction
In the world of machining, CNC lathes have emerged as a cornerstone technology, revolutionizing the manufacturing process with their speed, accuracy, and versatility. At HIRUNG, with over 20 years of experience in manufacturing CNC lathes, we have continuously evolved our products to meet the ever-increasing demands of the industry. Our EL series, the third-generation offering, stands as a testament to our commitment to innovation and quality. This article will delve into the various operations performed by CNC lathes and showcase how HIRUNG’s expertise and advanced manufacturing processes ensure top-notch performance.
2. Understanding CNC Lathes
2.1 What is a CNC Lathe?
CNC, which stands for Computerized Numerically Controlled, has transformed the lathe into a highly efficient and precise tool. These lathes are controlled by computer programs, allowing for rapid and accurate machining operations. Once the program is loaded, the machine can operate with minimal human intervention, making it ideal for both small-batch production and mass manufacturing.
2.2 The Significance of CNC Lathe Operations
The ability to perform a wide range of operations with utmost precision is what sets CNC lathes apart. From creating complex geometries to achieving tight tolerances, these machines are the go-to choice for industries requiring high-quality components.
2.3 HIRUNG’s Journey in CNC Lathe Manufacturing
Since our establishment in January 2015, HIRUNG has been dedicated to delivering superior CNC lathes. Our machines have found their way into 33 countries and regions, a testament to their quality and performance. We adhere to high standard manufacturing processes, ensuring that our CNC lathes outperform many other Chinese brands in terms of quality and precision.
3. Operations Performed by CNC Lathes
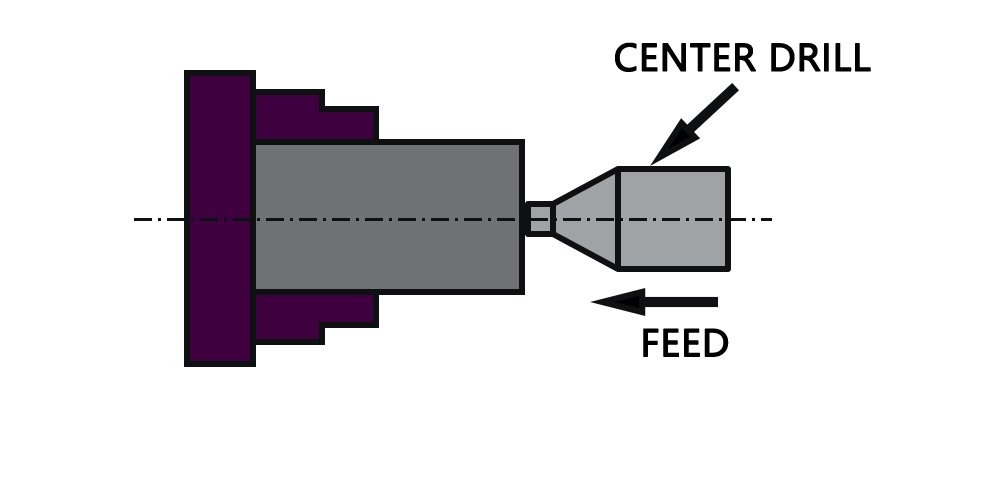
3.1 Centering
When a job needs to be held between two centers (headstock and tailstock), centering is crucial. It involves creating a conical hole in the face of the job to provide a stable bearing support for the lathe center. This operation lays the foundation for accurate machining.
3.2 Facing
The goal of facing is to produce a smooth flat surface on the ends of the workpiece. By using a three or four-jaw chuck to hold the workpiece on the headstock spindle and rotating it at the desired RPM, a perpendicular feed is provided to achieve the desired surface finish.
3.3 Turning
3.3.1 Straight Turning
This operation is used to create a cylindrical surface by removing excess material. The workpiece is secured, and the cutting tool is positioned parallel to or slightly above the work axis. With the spindle set to the appropriate feed rate and the depth of cut determined, the machining process begins. Automatic feed is then used to move the carriage with the tool along the workpiece until the task is completed.
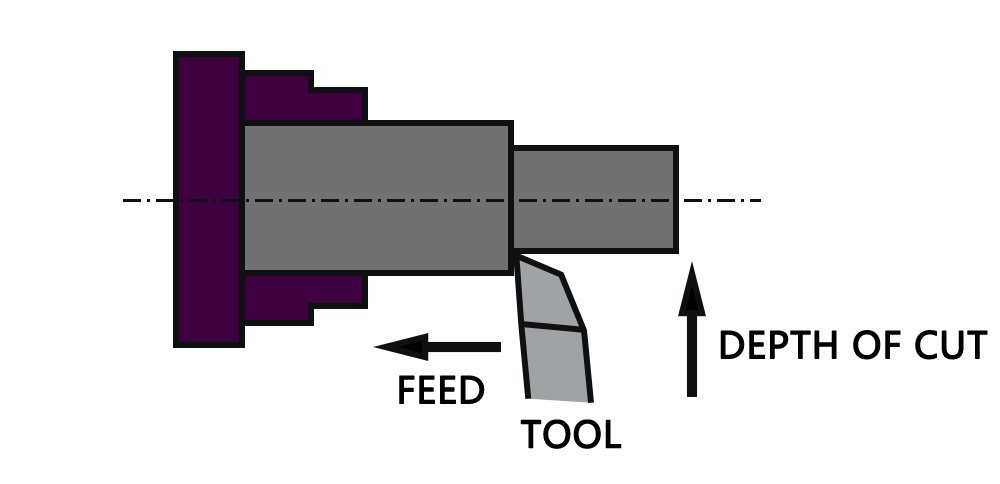
3.3.2 Rough Turning
For quickly removing a significant amount of material, rough turning is employed. It utilizes a high feed rate and a deep cut depth, typically ranging from 2 to 5mm, with a feed rate of 0.3 to 1.5mm per revolution.
3.3.3 Finish Turning
To achieve a smooth and precise surface, finish turning requires a high cutting speed, a low feed rate (0.1 to 0.3mm per revolution), and a shallow depth of cut (0.5 to 1mm).
3.3.4 Taper Turning
Tapered shapes can be created using various methods, such as using a form tool, swiveling the compound rest, resetting the tailstock, or employing a taper turning attachment.
3.4 Chamfering
Chamfering is essential for beveling the ends of the workpiece, removing burrs, enhancing appearance, and facilitating nut-bolt assembly. It is often performed before thread cutting, knurling, and rough turning.
3.5 Knurling
This operation creates a rough surface on the workpiece, improving grip. The knurling tool is firmly attached to the tool post and pressed against the rotating job, leaving an imprint of the tool on the surface.
3.6 Thread Cutting
Thread cutting is used to produce helical grooves on cylindrical or conical surfaces. The tool is fed longitudinally as the job rotates between the two centers, resulting in precise threads.
3.7 Drilling
Drilling allows for the creation of holes in the workpiece. The job is rotated on the lathe axis, and the drilling tool is mounted on the tail-stock spindle. The tail-stock is then manually fed towards the job to create the hole.
3.8 Boring
To increase the diameter of an existing hole, boring is performed using a boring tool. The tail-stock can also be equipped with a boring tool for this operation.
3.9 Reaming
Reaming is the process of using a reamer to achieve the final size and finish of a drilled hole. The reamer tool is attached to the tail-stock.
3.10 Spinning
In spinning, a sheet metal job is held between the former and the tail-stock center and rotated at high speed. A long round nose forming tool, fastened on a specific tool post, presses the work onto the periphery of the former, shaping it to the desired form without generating chips.
3.11 Tapping
This operation is used to create internal threads within a hole using a tap. Typically, three taps (taper tap, second tap, and plug tap) are used in sequence for optimal results.
3.12 Parting-Off
Once the machining process is complete, the parting-off operation cuts off the bar-type job. The bar is held in a chuck and rotated while a parting-off tool is slowly fed into the job until it reaches the center, separating the finished part from the raw material.
4. HIRUNG’s Commitment to Quality
At HIRUNG, we understand that the performance of a CNC lathe is not just about the operations it can perform but also about its reliability and durability. Our manufacturing processes are designed to ensure that each machine meets the highest standards. We focus on every aspect, from the initial design to the final assembly, and conduct rigorous quality checks at each stage. This attention to detail not only results in CNC lathes with exceptional accuracy and precision but also ensures their long-term stability and ease of maintenance.
In conclusion, CNC lathes are a marvel of modern manufacturing, capable of performing a wide array of operations with remarkable precision. HIRUNG’s EL series, with its advanced features and reliable performance, is at the forefront of this technology. Whether you are in the automotive, aerospace, or any other industry that demands high-quality machined parts, HIRUNG’s CNC lathes are designed to meet and exceed your expectations. Experience the HIRUNG difference and take your manufacturing capabilities to new heights.