In the world of CNC machining, mills and lathes are like master sculptors: one carves bold, intricate designs with precision, while the other crafts smooth, spinning curves with elegance. Whether you’re a hobbyist building custom parts, a student learning manufacturing, or a shop owner choosing equipment, understanding the difference between mill and lathe is key to picking the right tool. Mills and lathes shape everything from aerospace components to furniture legs, but their approaches differ fundamentally. Drawing on insights from HIRUNG expertise in precision CNC technology, this guide explores the mill vs lathe distinction—mechanics, applications, strengths, and more—to help you decide which machine suits your projects. Let’s dive into the heart of machining and uncover what sets these tools apart.
What is a CNC Mill?
A CNC mill is a powerhouse machine that uses rotating cutting tools to remove material from a stationary workpiece, creating flat surfaces, slots, or complex 3D shapes. It’s the go-to tool for intricate designs across industries, from automotive to electronics, offering versatility through multi-axis movement.

How It Works
The heart of a CNC mill is its spindle, a motor-driven shaft that spins cutting tools like end mills or drills at speeds ranging from 1,000 to 20,000 RPM, depending on the material (e.g., aluminum at 12,000 RPM, steel at 8,000 RPM). The workpiece—often a metal block, plastic sheet, or wood panel—is clamped to a table that moves along the X (left-right), Y (forward-back), and Z (up-down) axes. Advanced mills add A and B axes for 4- or 5-axis machining, enabling complex geometries. For example, milling a 0.5-inch slot in an aluminum plate with a ¼-inch end mill takes about 5 minutes per pass at 12,000 RPM. The process is guided by CNC software, ensuring precision to within 0.01 mm.
Applications
- Flat Surfaces: Smooth panels for machinery bases.
- Slots and Pockets: Keyways, bolt holes, or recesses for components.
- 3D Contours: Mold cavities, sculptures, or aerospace parts.
- Examples: Aluminum brackets for engines, plastic housings for circuit boards, steel molds for injection molding.
Advantages
- Versatility: Shapes diverse materials (metal, plastic, wood) into non-cylindrical forms.
- Precision: Achieves tolerances as tight as 0.01 mm, ideal for high-tech industries.
- Multi-Axis Capability: 5-axis mills tackle intricate designs with fewer setups.
Limitations
- Cylindrical Parts: Less efficient for round shapes, requiring multiple setups.
- Setup Complexity: Needs precise fixturing and programming, challenging for beginners.
- Cost: Basic CNC mills start at $5,000, with 5-axis models exceeding $50,000.
What is a CNC Lathe?
A CNC lathe is a specialized machine that rotates a workpiece against a stationary cutting tool to produce cylindrical or conical parts, such as shafts, threads, or bushings. It’s the tool of choice for anything round, offering speed and simplicity for symmetrical designs.

How It Works
In a CNC lathe, the workpiece—typically a metal rod, plastic bar, or wooden dowel—is clamped in a chuck or between centers and spun at speeds of 500 to 4,000 RPM. A single-point cutting tool, mounted on a movable turret, slides along the workpiece to remove material in a continuous, helical cut. For instance, turning a 3-inch steel rod to a 2-inch diameter shaft at 1,200 RPM takes about 6 minutes with a carbide insert. Modern CNC lathes often include live tooling, where rotating tools like end mills add milling capabilities (e.g., cutting slots on a spinning part). The process is controlled by CNC software, delivering surface finishes as smooth as Ra 0.8 μm.
Applications
- Shafts and Rods: For motors, axles, or rollers.
- Threads: External or internal threads for bolts, fittings, or screws.
- Bushings and Pulleys: For mechanical or automotive assemblies.
- Examples: Engine pistons, wooden furniture legs, threaded hydraulic connectors.
Advantages
- Speed for Round Parts: Completes cylindrical shapes in minutes, faster than mills for these tasks.
- Simplicity: Easier setup for symmetrical designs, ideal for beginners.
- Precision: Delivers tight tolerances (0.01 mm) and smooth finishes for round features.
Limitations
- Rotational Symmetry: Limited to cylindrical or conical shapes without live tooling.
- Less Versatile: Struggles with flat or complex non-cylindrical designs.
- Live Tooling Cost: Adding milling capabilities increases price and complexity.
Key Differences Between Mills and Lathes
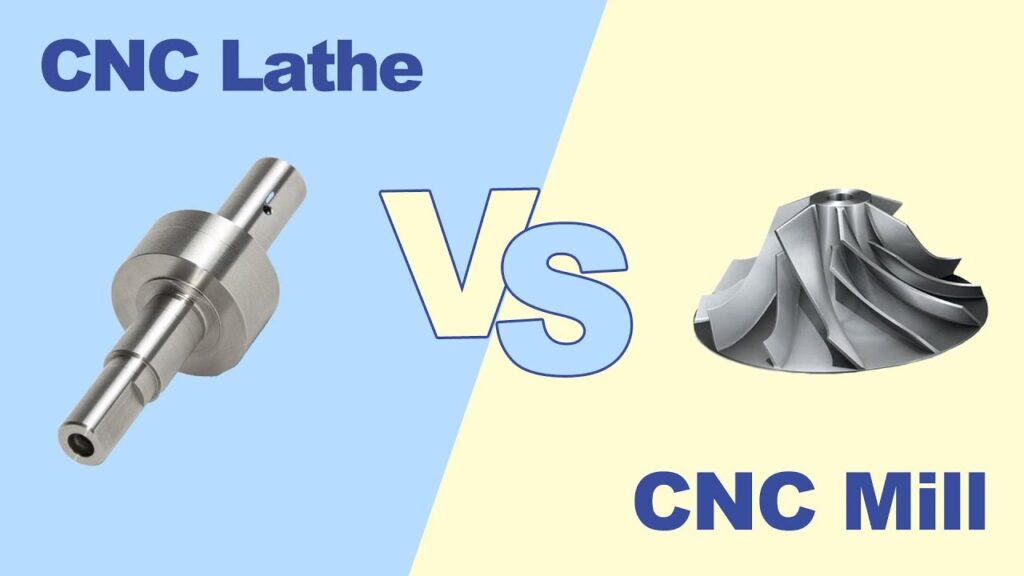
To choose between a CNC mill vs CNC lathe, you need to understand their core distinctions. Here’s a detailed comparison of their mechanics, applications, and practical considerations:
Operation Mechanics
- Mill: The cutting tool rotates (e.g., an end mill at 15,000 RPM), while the workpiece is stationary or moves linearly along multiple axes (X, Y, Z, A, B).
- Lathe: The workpiece rotates (e.g., a steel rod at 2,000 RPM), while the cutting tool moves linearly or remains fixed, shaping the spinning material.
Workpiece Handling
- Mill: Handles flat or block materials (e.g., aluminum sheets, steel plates) clamped to a table, moved in multiple directions for precise cuts.
- Lathe: Works with cylindrical or rod-shaped materials (e.g., brass bars, plastic tubes) spun in a chuck or between centers.
Tooling
- Mill: Uses multi-point cutters like end mills, face mills, or drills, secured with HSK or BT tool holders for stability (per ISO 7388 standards).
- Lathe: Employs single-point tools for turning, facing, or threading, with some CNC lathes using live tooling (e.g., rotating end mills) for milling tasks.
Applications
- Mill: Excels at flat surfaces, slots, pockets, and 3D contours, ideal for parts like control panels, mold bases, or circuit board housings.
- Lathe: Specializes in cylindrical or conical parts like shafts, bushings, or threaded components, perfect for mechanical or automotive assemblies.
Precision and Complexity
- Mill: Offers high precision for complex 3D geometries but requires advanced programming and fixturing, which can be daunting for new users.
- Lathe: Provides excellent precision for round parts with simpler setups, making it more approachable for beginners.
Cost and Space
- Mill: Typically more expensive ($5,000–$50,000 for CNC models) and requires a larger footprint, especially for multi-axis systems.
- Lathe: Often more affordable ($3,000–$20,000) and compact, fitting smaller workshops or home setups.
Comparison Table
This table summarizes the key differences for quick reference:
Feature | CNC Mill | CNC Lathe |
Operation | Tool rotates, workpiece stationary | Workpiece rotates, tool stationary |
Workpiece | Flat/block, multi-axis movement | Cylindrical, spun in chuck |
Tools | Multi-point (end mills, drills) | Single-point, optional live tooling |
Applications | Slots, pockets, 3D contours | Shafts, threads, bushings |
Precision | 0.01 mm for complex shapes | 0.01 mm for round parts |
Ease of Use | Complex setup, steeper learning curve | Simpler for beginners |
Cost | $5,000–$50,000 | $3,000–$20,000 |
Mill vs Lathe: Which Should You Choose?
Deciding between a mill or lathe depends on your project goals, skill level, and practical constraints. Here’s how to make the right choice:
Project-Based Considerations
- Choose a Mill:
- For flat, rectangular, or complex 3D parts, like a machined aluminum control panel with slots and holes.
- When versatility across materials (wood, metal, plastic) and shapes is critical.
- Example: Milling a 12” x 8” panel with 0.2-inch deep slots takes ~25 minutes on a 3-axis mill at 12,000 RPM.
- Choose a Lathe:
- For cylindrical or conical parts, like a steel shaft or threaded bolt.
- When speed and simplicity for round shapes are priorities.
- Example: Turning a 3-inch rod into a 2-inch pulley with M20 threads takes ~12 minutes at 1,200 RPM.
Skill Level
- Beginners: Lathes are often easier to learn due to their straightforward setup and focus on round parts. Basic CNC lathes with pre-programmed cycles simplify operation.
- Intermediate/Advanced Users: Mills offer more creative freedom for intricate designs but require skills in multi-axis programming and fixturing.
Budget and Space
- Budget-Conscious: Entry-level CNC lathes start at ~$3,000, making them more accessible for hobbyists or small shops. Mills typically start at $5,000, with advanced models much pricier.
- Space Constraints: Lathes are more compact, fitting small workshops or garages, while mills, especially multi-axis models, need larger spaces (e.g., 6’ x 6’ footprint).
Upgrading to Precision Solutions
As your skills and projects grow, you may need machines with tighter tolerances and advanced features. HIRUNG’s CNC mills and lathes are designed for this transition, offering:
- Precision: Tolerances below 0.01 mm, ideal for aerospace, automotive, or medical parts.
- Cost-Effectiveness: Priced up to 30% lower than comparable high-end brands, delivering value without compromise.
- Versatility: Models with live tooling or 5-axis capabilities for complex, multi-process tasks. When ready to upgrade, explore HIRUNG’s solutions at www.hirung.com or contact hirung@hirung.com for tailored options.
Practical Examples
To bring the CNC mill vs lathe comparison to life, here are three real-world scenarios showcasing their applications:
Milling Example: Aluminum Control Panel
- Task: Create a 12” x 8” aluminum panel with 0.2-inch deep slots and 0.25-inch bolt holes for an electronics housing.
- Machine: 3-axis CNC mill with a 3 kW spindle and BT30 tool holder.
- Process: Use a ¼-inch end mill at 12,000 RPM to cut slots, followed by a drill for holes. Total time: ~25 minutes, including setup and tool changes.
- Why a Mill?: Efficiently handles flat surfaces and precise cutouts, unfeasible on a lathe.
Lathe Example: Steel Motor Shaft
- Task: Turn a 3-inch diameter steel rod into a 2-inch diameter shaft with an M20 threaded end.
- Machine: CNC lathe with a 2 kW spindle and carbide turning tool.
- Process: Spin the rod at 1,200 RPM, reduce diameter in multiple passes, and cut threads. Total time: ~12 minutes.
- Why a Lathe?: Fast and accurate for cylindrical shapes, outperforming a mill for this task.
Combined Use: Bushing with Live Tooling
- Task: Produce a steel bushing with a 2-inch outer diameter, 1-inch internal bore, and a milled keyway.
- Machine: CNC lathe with live tooling.
- Process: Turn the outer diameter and bore at 1,000 RPM, then use a live end mill at 8,000 RPM to cut the keyway. Total time: ~15 minutes.
- Why Both?: Live tooling combines turning and milling, reducing setups and enhancing efficiency.
Tips for Beginners
Starting with mills or lathes can be exciting yet daunting. These tips will help you dive in with confidence:
- Start Simple: Practice with basic projects to learn machine capabilities. Mill a flat wooden plaque or turn a small aluminum rod to understand feeds and speeds.
- Learn Software: Use Easel (free, web-based) for milling simple designs or Fusion 360 (free for hobbyists) for both mills and lathes. Explore YouTube tutorials (e.g., search “CNC milling basics”) for step-by-step guidance.
- Prioritize Safety: Wear goggles, secure workpieces tightly, and follow machine manuals to avoid accidents. Check spindle and tool conditions before starting.
- Experiment with Tooling: Try different cutters, like 1/8-inch end mills for mills or carbide inserts for lathes, to see their impact on finish and speed.
- Tap into Resources: Visit Instructables for project ideas (e.g., “CNC lathe projects”) or join forums like Reddit’s r/CNC to connect with other machinists.
Conclusion
The mill vs lathe debate hinges on one core difference: mills shape flat or complex parts with rotating tools, while lathes craft cylindrical components by spinning the workpiece. Mills offer unmatched versatility for slots, pockets, and 3D designs, ideal for intricate projects. Lathes excel at speed and simplicity for shafts, threads, and bushings, making them beginner-friendly. Choose based on your project’s shape, your skill level, and your budget—mills for complexity, lathes for round parts. Start with an entry-level machine to build skills, and when you’re ready for professional-grade precision, explore HIRUNG’s CNC mills and lathes, delivering 0.01 mm tolerances at up to 30% lower costs than competitors. Begin your machining journey today—contact hirung@hirung.com to take your projects to the next level!