In a rapidly evolving manufacturing landscape, CNC (Computer Numerical Control) machines have become indispensable tools for creating precision parts and components. They streamline production by automating the movement of cutting tools along specific paths, guided by advanced software and controllers. Of the many types of CNC machines available, two configurations—3-axis and 5-axis CNC machines—are especially relevant for those looking to balance complexity, budget, and efficiency. In this article, we’ll delve into the fundamentals of CNC technology, explore the distinctions between 3-axis and 5-axis CNC setups, and help you determine which one best meets your manufacturing needs.
Whether you’re a small workshop owner aiming to expand your capabilities or a large-scale operation leader evaluating new investments, understanding the nuances of 3 axis 5 axis cnc machine setups will be critical. You’ll discover the advantages, limitations, and latest trends shaping these technologies, empowering you to make well-informed decisions that will drive your production goals forward.
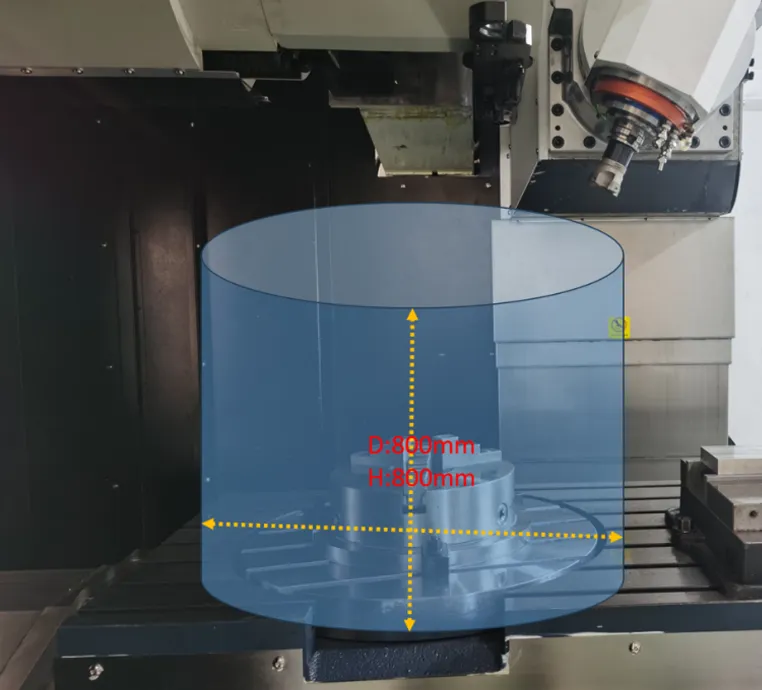
I. Overview of CNC Machining
Definition and Brief History of CNC
CNC machining is a computerized process that uses pre-programmed software and code to control the movement of manufacturing equipment. It traces its roots back to the mid-20th century, when numerical control methods were first used in machine tools. Over time, these control methods were refined and integrated with modern computing technologies, giving birth to CNC machines.
Today, CNC machining is widely used across countless industries—from aerospace and automotive to electronics and medical—and is cherished for its precision, reliability, and scalability. By automating tasks once performed by hand, CNC machines dramatically increase production speed while reducing human error.
Basic Components of a CNC Machine
While CNC machines come in all shapes and sizes, they typically share a few core components:
- Controller: The “brain” of the machine, which executes the pre-programmed code.
- Motors and Drives: Control the movement along various axes.
- Machine Bed or Table: The surface on which the material or workpiece is placed.
- Cutting Tool or Spindle: Performs the actual cutting, drilling, milling, or turning operation.
- Software Interface: Allows operators to write or upload G-code and M-code, the languages that direct the machine’s movements.
Significance in Various Industries
- Aerospace: Fabricating complex, lightweight parts with tight tolerances.
- Automotive: Mass-producing car parts such as engine components and transmissions.
- Medical: Creating implants, surgical tools, and precise instruments.
- Electronics: Milling circuit boards or enclosures with high accuracy.
CNC technology plays a vital role in manufacturing high-quality products at scale. It ensures repeatability, reduces scrap, and handles intricate geometries that might otherwise be too difficult or impossible to produce with manual techniques.
II. What is a 3-Axis CNC Machine?
Working Principles
A 3-axis CNC machine operates along three linear axes: X, Y, and Z. These axes describe the tool’s movement in a straight line from left to right (X-axis), front to back (Y-axis), and up and down (Z-axis). This relatively straightforward design makes the 3-axis machine both accessible and budget-friendly, making it an ideal starting point for smaller workshops or operations focused on simpler parts.
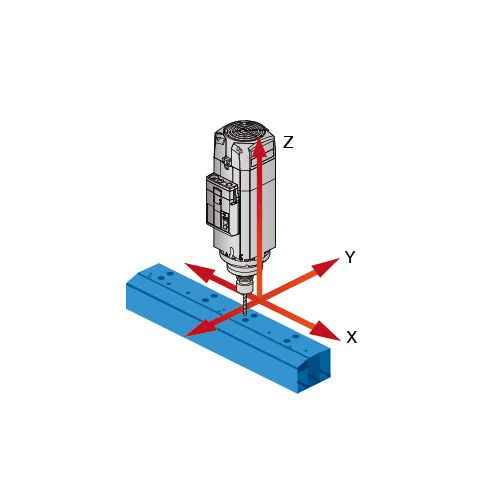
The typical process flow for a 3-axis CNC machine involves:
- Securing the workpiece on the machine bed.
- Setting up the appropriate cutting tool.
- Running the programmed toolpath, which may include drilling, milling, or any combination of subtractive steps.
Although 3-axis CNC machining may appear limited, experienced operators can still achieve impressive accuracy and speed with a well-optimized toolpath.
Common Applications
3-axis CNC machines are used to produce components such as:
- Flat or 2.5D Parts: Plates, brackets, or simple mold cavities.
- Housings and Enclosures: Consumer products, electronic device shells, and basic mechanical enclosures.
- Rapid Prototyping: Generating quick prototypes where complex curves or undercuts are minimal.
Advantages and Limitations
Advantages
- Cost-Effective: 3-axis machines usually have a lower price point than their 5-axis counterparts.
- Easier to Operate: Simpler programming and fewer variables to manage.
- Wide Availability: There’s a large market for both new and used 3-axis machines.
Limitations
- Restricted Geometries: Unable to access certain angles or complex undercuts without multiple re-fixtures.
- Longer Setup Times: May require repositioning the workpiece to handle multiple faces.
- Less Versatile: Not well-suited for manufacturing highly complex parts.
III. What is a 5-Axis CNC Machine?
Working Principles
A 5-axis CNC machine adds two rotational axes to the three linear axes, typically referred to as the A- and B-axes, or B- and C-axes, depending on the machine configuration. These rotational axes allow the cutting tool or the workpiece to tilt and rotate in a way that enables the tool to reach almost any surface of the part.
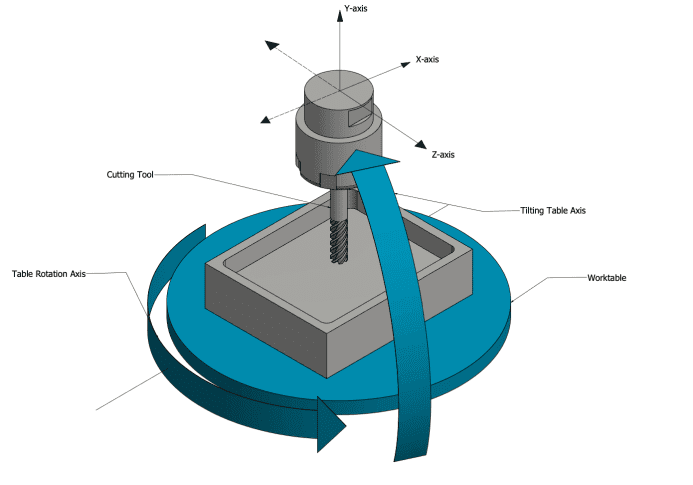
In essence, the machine can move in all three linear directions while also rotating either the spindle or the table to process complex angles without removing the workpiece and re-clamping. This capability makes 5-axis CNC machines a top choice for intricate geometries.
There are several configurations of 5-axis machines, such as:
- Head/Head: Both A-axis and B-axis are on the spindle or milling head.
- Head/Table: The spindle can tilt in one axis, while the table rotates in another.
- Table/Table: The table tilts in one axis and rotates on another axis.
Common Applications
5-axis machines are integral to industries that demand high precision on complex shapes, such as:
- Aerospace: Turbine blades, engine components, and structural aircraft parts.
- Medical: Orthopedic implants, prosthetics, and surgical instruments.
- Automotive Racing: Prototype engine blocks and performance parts with specialized geometry.
Advantages and Limitations
Advantages
- Unmatched Geometric Freedom: Ability to create parts with complex angles, undercuts, and intricate surfaces.
- Reduced Setup Times: Often eliminates the need to reposition the workpiece multiple times.
- Improved Surface Finish: Continuous cutting from multiple angles can yield better finishes and fewer tool marks.
Limitations
- Higher Cost: Purchase, operation, and maintenance costs exceed those of simpler machines.
- Programming Complexity: Requires advanced CAM software and experienced operators to optimize results.
- Longer Learning Curve: The extra degrees of motion demand more specialized training.
IV. Key Differences Between 3-Axis and 5-Axis CNC Machines
When deciding between a 3-axis CNC machine and a 5-axis CNC machine, it’s essential to factor in these critical differences:
- Setup Time:
- 3-Axis: Often requires multiple fixturing setups to handle different faces, increasing production time.
- 5-Axis: Can handle complex parts in a single setup, substantially reducing total machine time.
- Production Efficiency:
- 3-Axis: Efficient for simpler parts, but more labor-intensive for geometrically complex tasks.
- 5-Axis: Reduces manual intervention, improves cycle times for intricate parts.
- Complexity of Parts:
- 3-Axis: Best suited for flat surfaces, 2.5D profiles, and moderately complex parts.
- 5-Axis: Handles undercuts, contoured surfaces, and sophisticated geometries with ease.
- Cost:
- 3-Axis: Lower initial investment and simpler maintenance.
- 5-Axis: Higher upfront costs but potential for faster ROI if complex, high-value parts are produced regularly.
- Skill Level Required:
- 3-Axis: More accessible to beginners, shorter learning curve.
- 5-Axis: Needs advanced CAM software knowledge, more experienced programmers/operators.
Selecting the right CNC solution comes down to balancing the scope of your projects with your budget and technical capabilities. Some operations can thrive on 3-axis machines alone, while others require the multifaceted approach of a 5-axis setup.
V. How to Choose the Right CNC Machine
Choosing between a 3-axis and a 5-axis CNC machine is one of the most critical decisions in a manufacturing operation. Below are key considerations:
1. Project Requirements and Complexity
- Part Geometry: If you’re frequently working on parts with complex curves, multiple faces, and tight tolerances, you’ll likely need the flexibility of a 5-axis machine. If most of your projects revolve around simpler shapes, a 3-axis machine could suffice.
- Industries Served: Certain industries—such as aerospace, defense, and medical—often require extremely high precision and complex part designs. This makes a 5-axis machine almost indispensable.
2. Budget and Return on Investment
- Initial Capital Expenditure: A 5-axis CNC machine typically comes with a higher price tag. However, if you’re certain your production volume and complexity warrant this technology, the long-term payoffs in efficiency and part quality can justify the cost.
- Operational Costs: Beyond the purchase price, factor in training, tooling, software licensing, and maintenance.
- Volume and Scalability: If you anticipate growing demand or expanding into advanced markets, investing in a 5-axis machine upfront may prevent costly upgrades later on.
3. Skill and Training
- Operator Expertise: Operating a 5-axis machine requires a deeper understanding of CAM software, tool motion, and collision avoidance. If you have or plan to hire skilled personnel, this is feasible. If not, you may face a steep learning curve.
- Software Requirements: Advanced or specialized CAM programs are often needed for 5-axis programming. Ensure you have access to robust software tools.
4. Future-Proofing Your Operations
- Industry Trends: Technologies evolve rapidly. A 5-axis machine might give you a competitive edge and open up new business opportunities.
- Flexibility: Even if your projects today are simpler, having the ability to tackle complex parts can attract higher-end clients and projects.
VI. Future Trends in CNC Technology
The world of 3 axis 5 axis cnc machine solutions is continually progressing, shaped by digital innovation and changing market needs. Here are some developments worth watching:
- Automation and Robotics
- Collaborative robots (cobots) and robotic arms are being integrated into CNC processes to speed up loading/unloading and reduce labor costs.
- Automated tool changers and pallet changers further improve efficiency and minimize downtime.
- Smart Manufacturing and IoT
- Advanced CNC machines now come equipped with sensors that track temperature, vibrations, and spindle loads.
- This data can be analyzed to predict tool wear, enhance part quality, and optimize machining parameters in real time.
- AI-Driven CAM Software
- Machine learning algorithms are helping optimize toolpaths, reduce cycle times, and minimize errors.
- Adaptive machining, where the CNC machine adjusts its own parameters based on live feedback, is gaining traction.
- Additive-Subtractive Hybrids
- Some manufacturers are developing machines that combine CNC milling with additive manufacturing techniques like 3D printing.
- This integration allows for more complex parts to be built and finished in a single environment.
- Remote Monitoring and Digital Twins
- Operators can monitor machine performance from anywhere, receiving alerts about maintenance or process errors instantly.
- Digital twins replicate the physical CNC environment in a virtual model, enabling advanced simulations and process optimizations.
As these trends transform the manufacturing world, both 3-axis and 5-axis CNC machines will continue to provide critical functionalities for different segments of the market. Staying ahead of these trends can help businesses maintain a competitive edge.
VII. Conclusion
3-axis CNC machines excel in cost-effectiveness and simplicity, making them a solid choice for basic to moderately complex parts. 5-axis CNC machines, on the other hand, cater to intricate designs, advanced manufacturing demands, and streamlined workflows. The question of which machine to invest in depends largely on your product complexity, volume, budget, and desired precision.
Companies that focus on mass production of less complex parts may stick with 3-axis setups, optimizing processes to achieve the lowest cost per unit. Meanwhile, firms aiming for the high-end market, dealing with specialized industries, or forging into R&D for cutting-edge components will find that the 5-axis approach is not just a luxury but often a necessity.
In today’s competitive environment, the ability to adapt to rapidly shifting customer needs and technological advancements can make or break a manufacturing operation. Thus, investing in a CNC solution is not simply about the immediate cost or capabilities, but also about positioning your business for future growth. When carefully evaluated, both 3-axis and 5-axis CNC machines can play pivotal roles in delivering consistent, high-quality parts that meet the rigorous standards of modern industry.
VIII. About Our Company
If you’re looking for guidance on investing in 3 axis 5 axis cnc machine technology—whether you need a straightforward 3-axis setup or a high-performance 5-axis solution—we are here to assist. Our dedicated team specializes in helping businesses identify the right CNC solutions, streamline their manufacturing processes, and integrate new technology seamlessly. With a focus on precision, efficiency, and long-term client success, our company’s approach to CNC technology and comprehensive after-sales support sets us apart in the industry. We invite you to contact us to learn how we can help you achieve new levels of productivity and quality in your manufacturing operations.
By aligning our expertise with your goals, we aim to empower your business to excel in a rapidly evolving manufacturing landscape.